News Type
Publication Date
2219 results found
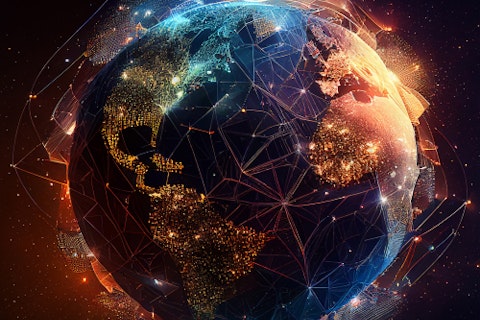
Acquisition of ArcLight Wireless Inc.
This acquisition, effective May 1, 2024, allows us to expand our footprint in North America and strengthen our leadership in the dynamic connectivity industry.
Read more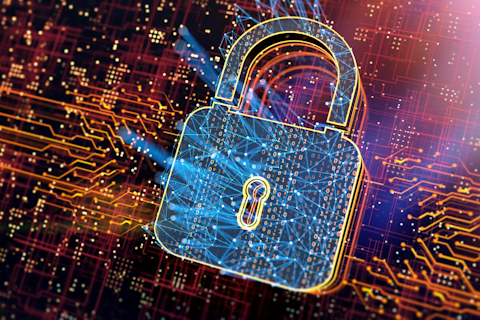
UK PSTI Enforcement Date Approaches
UK Product Security and Telecommunications Infrastructure (PSTI) regulations will be fully enforced and mandatory for IoT manufacturers selling on UK markets from April 29, 2024.
Read more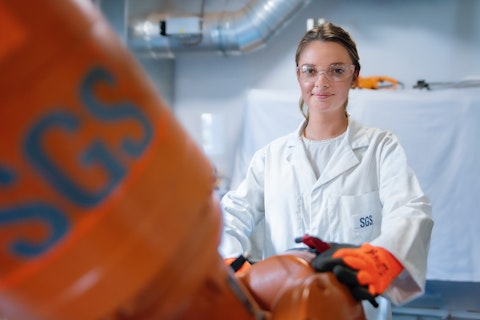
First Quarter 2024 Sales Update
We are pleased to announce a strong start to the year, with Strategy 2027 on track.
Read more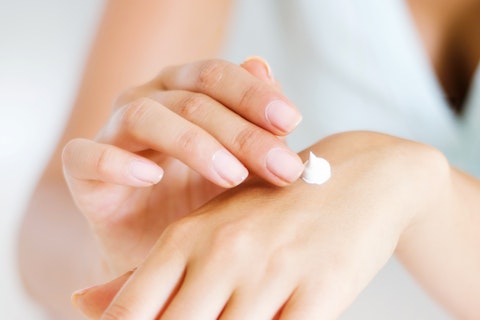
Skin Barrier – Function, Restoration and Repair
Our clinical scientists operate at the forefront of skincare innovation.
Read more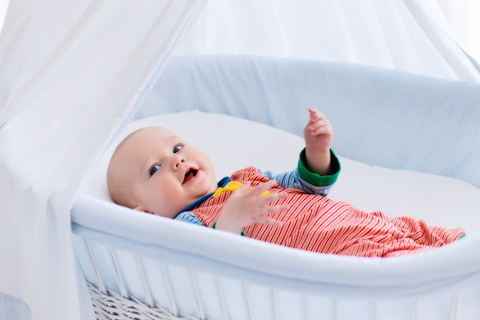
US CPSC Issues Notice of Proposed Rulemaking for Bassinets and Cradles
US Consumer Product Safety Commission (CPSC) has published a notice of proposed rulemaking to revise the existing consumer product safety rule for bassinets and cradles.
Read more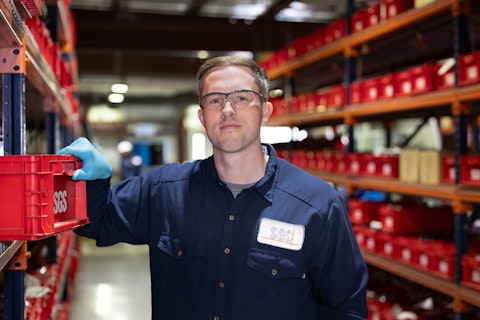
Dividend 2023: Announcement of Final Terms
SGS announces today that 64.87% of the dividend for the financial year 2023 was elected to be paid in the form of new SGS shares, while the remaining 35.13% will be paid out in cash.
Read more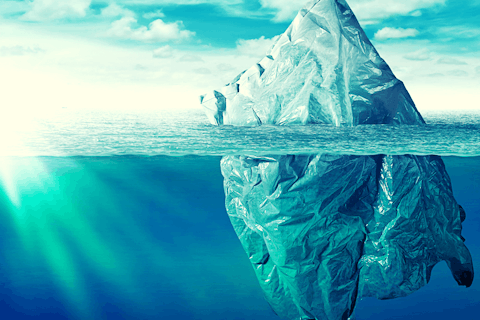
Defining the New ISO 14068-1 Carbon Neutrality Standard
What is ISO 14068-1 and how can it help you show your carbon neutrality?
Read more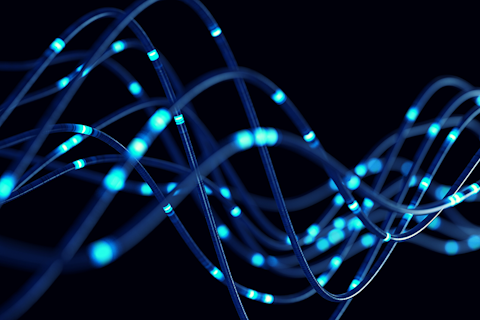
NIS2 is Near, So Let’s Make Things Clear
The European Union’s NIS2 is set to become law in member states by October 2024, so what do you need to know?
Read more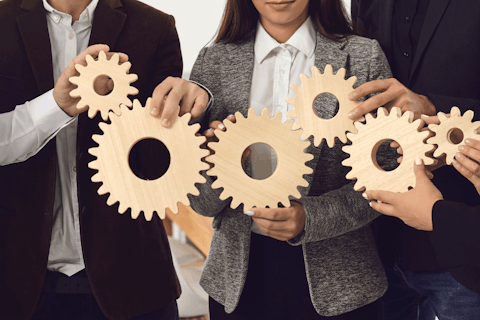
The Lean Management System, from Strategy to Excellence
We take you through Lean management, from strategizing to the end goal.
Read more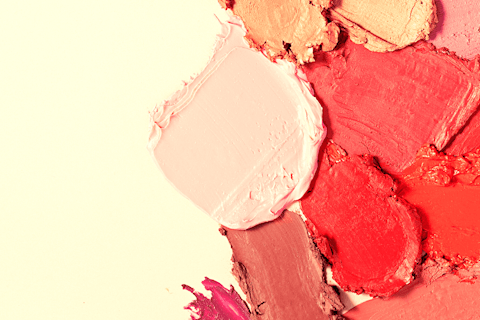
Proud to be an Accredited ISO 22716 Certification Body
We provide ANAB-accredited ISO 22716 certification, covering personnel, technology and administrative management that will affect product quality.
Read more