SGS was awarded one of the major shutdown projects by the energy company in Iraq. However due certain circumstances, the client preferred to inspect the integrity of their equipment well before the planned shutdown.
Inspection approach and challenge
SGS suggested to perform non-intrusive inspections as the client desired to complete the health assessment of assets months before the actual shutdown. However, another challenge was to perform inspection of a large number of equipment along with administrative activities including reporting in very short interval of time.
Why non-intrusive inspection?
During the whole lifecycle of plant, pressure vessels undergo periodic, statutory, and other testing to ensure continued safe and reliable operation. These inspections are carried out by means of internal visual inspection (IVI) with shutting down the vessel.
However, there can be very high costs associated with shutting down a vessel (loss of production), isolating it and preparing it for entry. Furthermore, the mechanical disturbances involved in preparing the vessel for internal inspection and reinstating it may adversely affect its future performance.
Therefore, performing inspection from the outside of the vessel without breaking containment i.e., non-invasively is a much-sophisticated approach than internal inspections.
Benefits of non-intrusive inspection
- Reduced production losses associated with shutdown
- Reduced manpower requirements - this can lead to reduced shutdown cost and shorter overall shut-down times since greater capacity is available for other tasks
- Removal of hazards associated with man entry of vessels
- Removal of the need to clean vessels internally
- Possibility to carry out the inspection when a potential problem is identified, without interfering with other operations
- Result of such inspection can be used to optimize the conclusion about which parts need to be replaced or may be prefabricated to minimize the time needed for placement during shutdown
How have we made it possible?
To meet the strict timeline a team of 35 members was established, including 24 multiskilled API/NDT inspectors to complete the whole task within agreed timeline.
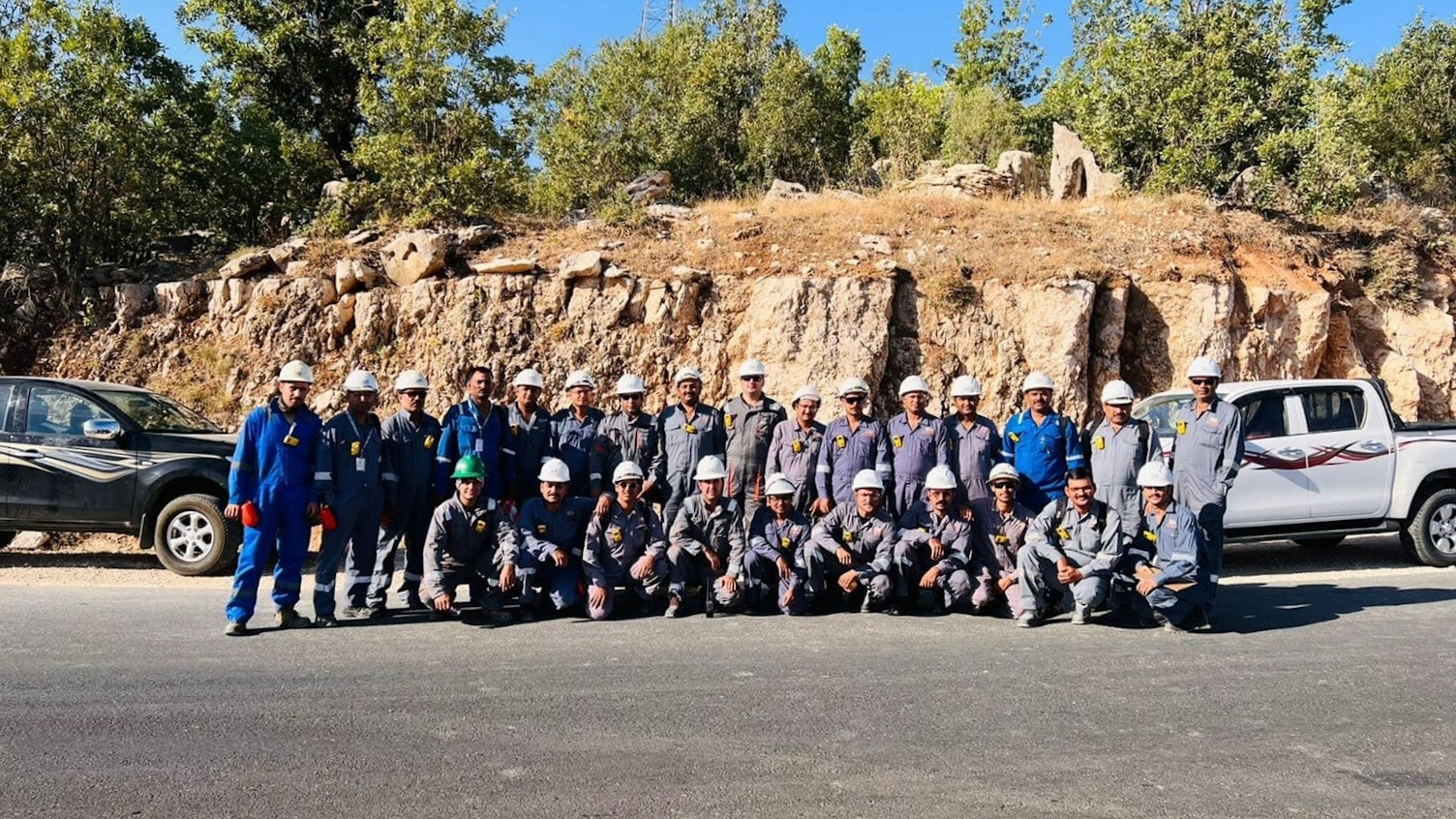
During inspection the following techniques were used:
- Visual inspections (API 510)
- Ultrasonic thickness (UT) gauging
- Time of line diffraction (ToFD)
- Ultrasonic flaw detection (UFD)
- Phased array ultrasonic testing (PAUT)
- Short range ultrasonic testing (SRUT)
- Automated Corrosion mapping
- Surface eddy current testing (SECT)
Conclusion
With strong expertise and unwavering determination of the entire team, the job was completed non-instructively using advance NDT techniques, well ahead of the conventional inspection.
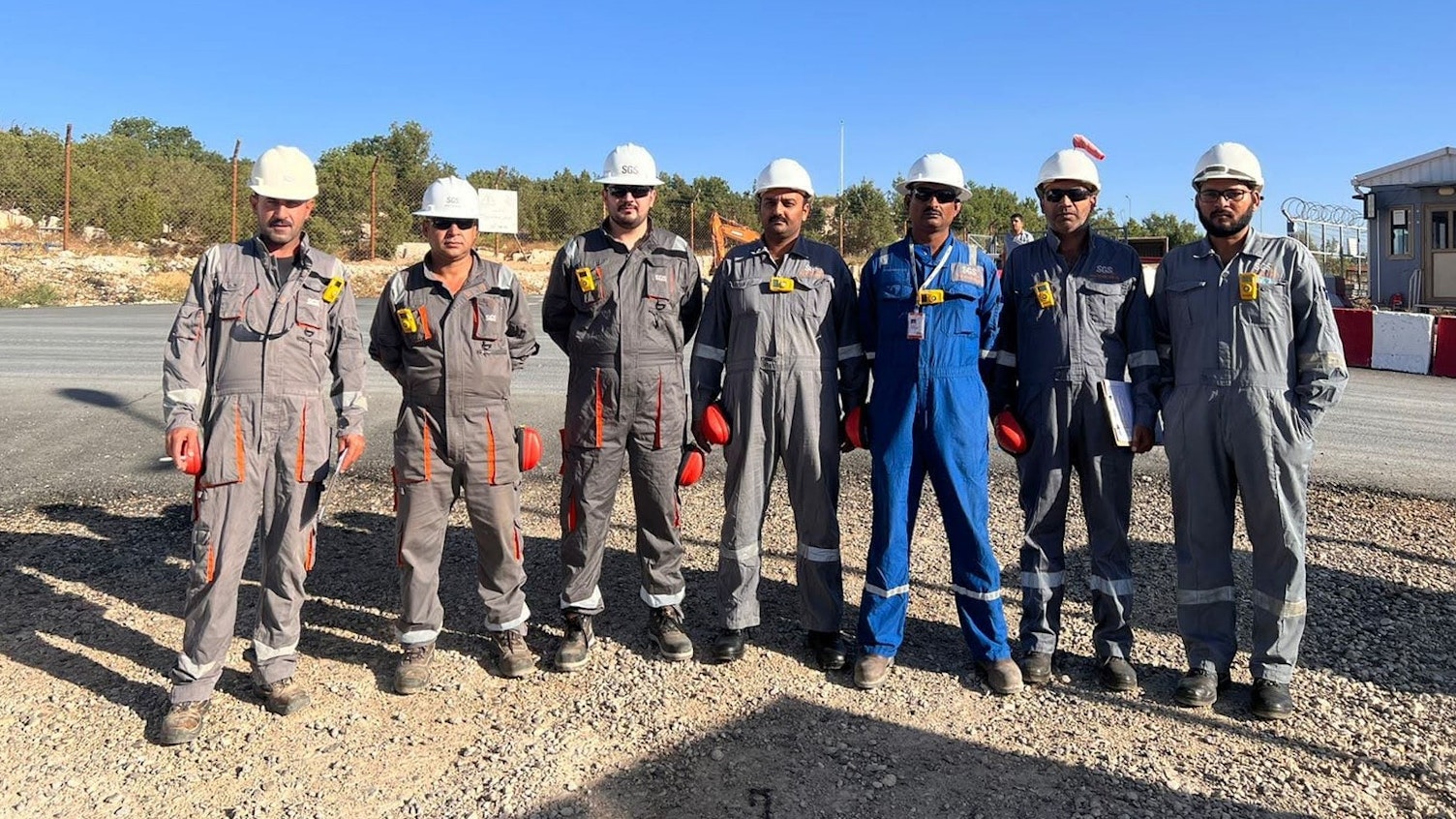
About SGS
We are SGS – the world's leading testing, inspection and certification company. We are recognized as the global benchmark for sustainability, quality and integrity. Our 99,600 employees operate a network of 2,600 offices and laboratories, working together to enable a better, safer and more interconnected world.
Amman, Al-Jbeiha, Yajouz Street,
Caracas Building, Entrance No1, 3rd Floor, Office 311, 11193,
Amman, Jordan